Pressage
Des presses à balles cubiques toujours plus performantes
Les dernières générations de presses à balles cubiques marquent une évolution vers des débits de chantier accrus et des balles plus denses.
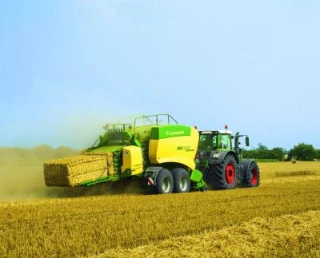
Ces dernières années, les presses haute densité ont vu leur débit de chantier augmenter sans dégrader la qualité de pressage, notamment en dimensions 120 x 70 cm et 120 x 90 cm, majoritairement demandées sur le marché de la paille. La première évolution concerne la cadence du piston, qui atteint désormais 45 à 51 coups par minute. Soit un rythme accru de 15 à 20 %. Cette évolution s’accompagne bien souvent d’un accroissement de la longueur du canal, voire d’une course de piston plus importante. Avec ce rythme plus soutenu, l’ensemble de la cinématique a été consolidé. Le volant d’inertie a été alourdi et redessiné, avec une translation de la masse vers la périphérie, pour gagner en inertie. Au niveau du pick-up, pour obtenir un flux de matière constant, les rouleaux tasse-andain et les dispositifs de recentrage se sont généralisés. Le rotor évolue également vers des gros diamètres de 550, 600, voire 860 mm. Plus lourd, il dispose d’une forte inertie qui diminue les pics de charge et de consommation.
Du côté de la chambre de précompression, la majorité des constructeurs proposent aujourd’hui des presses offrant le choix entre une alimentation régulière du canal ou un système automatisé attendant le remplissage complet de la chambre de précompression avant d’alimenter le canal : généralement, le chauffeur choisit en cabine le mécanisme d’amenage qui lui convient, le second système convenant mieux aux andains petits ou irréguliers.
L’ensemble de ces évolutions a permis d’accroître les débits de chantier de 10 à 20 %. Pour tracter ces machines hautes performances à plein régime, les besoins de puissance se sont naturellement accrus, tout en réduisant la consommation de carburant à l’hectare.
[INTER]Vers la très haute densité[inter]
Pour répondre à une certaine demande du marché, Krone et Massey Ferguson ont développé des presses en format 120 x 90 centimètres offrant une densité plus élevée, avec des balles de paille atteignant 500 à 550 kg au lieu de 400. Une fois chargés, les camions sont plus lourds de 5 à 7 tonnes, ce qui rentabilise davantage chaque voyage.
Pour atteindre cette densité, les presses ont été renforcées et surdimensionnées, avec des poids pouvant dépasser les 15 tonnes : les besoins de puissance de traction et d’entraînement sont bien entendu plus élevés.
Cependant, ces bottes à très haute densité ne s’adressent pas à tous les publics, les éleveurs refusant les densités supérieures à 160 kg/m3, car elles posent des problèmes de reprise par les pailleuses.
Proposé par une majorité de constructeurs, le capteur d’humidité est très demandé sur les presses à très haute densité, mais également de plus en plus plébiscité sur les machines classiques. Il permet de valider les bonnes conditions de récolte, mais aussi de détecter le moment où la rosée tombe.
Autre option de plus en plus demandée, le capteur de pesée. Monté en sortie de canal, il affiche généralement une précision de 98 % et permet donc de valider la densité souhaitée. Au cours de la journée, le poids d’une balle varie pour un même réglage de densité, atteignant son seuil le plus bas aux heures les plus chaudes. Le système de pesée permet ainsi au chauffeur de moduler les réglages de pressage tout au long de la journée pour avoir des balles de poids requis.
Du côté de la chambre de précompression, la majorité des constructeurs proposent aujourd’hui des presses offrant le choix entre une alimentation régulière du canal ou un système automatisé attendant le remplissage complet de la chambre de précompression avant d’alimenter le canal : généralement, le chauffeur choisit en cabine le mécanisme d’amenage qui lui convient, le second système convenant mieux aux andains petits ou irréguliers.
L’ensemble de ces évolutions a permis d’accroître les débits de chantier de 10 à 20 %. Pour tracter ces machines hautes performances à plein régime, les besoins de puissance se sont naturellement accrus, tout en réduisant la consommation de carburant à l’hectare.
[INTER]Vers la très haute densité[inter]
Pour répondre à une certaine demande du marché, Krone et Massey Ferguson ont développé des presses en format 120 x 90 centimètres offrant une densité plus élevée, avec des balles de paille atteignant 500 à 550 kg au lieu de 400. Une fois chargés, les camions sont plus lourds de 5 à 7 tonnes, ce qui rentabilise davantage chaque voyage.
Pour atteindre cette densité, les presses ont été renforcées et surdimensionnées, avec des poids pouvant dépasser les 15 tonnes : les besoins de puissance de traction et d’entraînement sont bien entendu plus élevés.
Cependant, ces bottes à très haute densité ne s’adressent pas à tous les publics, les éleveurs refusant les densités supérieures à 160 kg/m3, car elles posent des problèmes de reprise par les pailleuses.
Proposé par une majorité de constructeurs, le capteur d’humidité est très demandé sur les presses à très haute densité, mais également de plus en plus plébiscité sur les machines classiques. Il permet de valider les bonnes conditions de récolte, mais aussi de détecter le moment où la rosée tombe.
Autre option de plus en plus demandée, le capteur de pesée. Monté en sortie de canal, il affiche généralement une précision de 98 % et permet donc de valider la densité souhaitée. Au cours de la journée, le poids d’une balle varie pour un même réglage de densité, atteignant son seuil le plus bas aux heures les plus chaudes. Le système de pesée permet ainsi au chauffeur de moduler les réglages de pressage tout au long de la journée pour avoir des balles de poids requis.